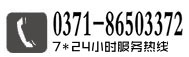
设计入口参数,烟气量工况144万m3/h,入口二氧化硫浓度1000mg/nm3,入口颗粒物排放浓度120mg/nm3;设计出口参数,颗粒物20mg/nm3,氮氧化物300mg/nm3。
原脱硫系统采用石灰.石膏湿法脱硫工艺,一机一塔,配备一台增压风机,烟气经增压风机引至烟气脱硫系统,进入吸收塔进行脱硫反应。氮化硅在吸收塔内烟气脱硫吸收塔为喷淋空塔,烟气垂直进入吸收塔,然后折向朝上流动并经塔内烟气整流器整流后,与喷淋而下的浆液进行充分接触以脱除其中的s0,,在吸收塔内烟气中的so,被吸收浆液洗涤并与浆液中的脱硫剂发生反应,反应生成的亚硫酸钙在吸收塔内底部的循环浆池内被氧化风机鼓入的空气强制氧化,最终生成石膏,石膏浆液排至石膏浆液池,送入脱硫副产品处理回收系统。脱硫后的洁净烟气经除雾器通过塔上直排烟囱直排。脱硫系统主要包括烟气系统、吸收系统、除尘系统、工艺水系统、副产物处理系统、电气及控制系统、能源动力介质系统以及自动化控制系统等主要系统。主要设备有:石灰粉仓及支架等附件、增压风机、吸收塔及塔内外附件、吸收塔循环泵、隔膜箱式压滤机、石膏池搅拌器、石灰池搅拌器、吸收塔搅拌器、供浆泵、中的so—碳化硅喷嘴石膏浆液泵、滤液输送泵、工艺水泵、除雾器冲洗水泵等。
面对日益严峻的环保形势,国家及地方环保新标准对烧结机脱硫系统的可靠、高效、连续运行提出了更高要求,永泉工贸经过近一年多的考察后碳,对二氧化硫及粉尘等污染物排放浓度的要求也日趋严格。早期建设的脱硫设施已无法满足新标准的要求,原建设的脱硫设施必须通过提效改造来实现颗粒物、二氧化硫的达标排放。文章对如何在改造过程中最大限度的缩短工期、充分利用原有设备减少建设投资实现达标排放等做了充分考虑。
脱硫系统设计烟气量工况144万1t13/h,入口二氧化硫浓度1000mg/nm3,入口颗粒物排放浓度120mg/nm3,出口设计排放浓度颗粒物50mg/nm3,二氧化硫200mg/nm3,氮氧化物300mg/nm3。自2012年5月投运至改造前,脱硫系统运行稳定,净烟气so:排放浓度满足环保要求。2015年1月1日起执万方数据口圜困圈圈口行的新标准要求颗粒物30mg/nm3,二氧化硫100mg/nm3,氮氧化物300mg/nm3,原脱硫系统通过运行负荷调整以及烧结机入口原燃料硫份控制,基本能够实现达标排放。入口二氧化硫控制在1000mg/nm3以内时,出口二氧化硫基本都能实现达标排放,但是颗粒物排放呈现超标。见表1。
新增循环泵接入口管道穿过输料廊支架,故将输料廊支架底部一组剪刀撑改造,剪刀撑避开新增循环泵接入口管道,以保证输料廊支架结构稳定性及便于新!
脱硫提效改造重点分两部分:一是降低二氧化硫排放浓度,二是降低粉尘排放浓度来实现污染物的综合达标排放。降低二氧化硫排放浓度,最直接的办法就是增加塔内脱硫浆液的循环量,原有三层喷淋层,每层对应一台浆液循环泵。所以改造首先增加一层喷淋层以及对应的循环泵等相关系统,以此增大塔内的浆液循环量,降低二氧化硫排放浓度。降低出口颗粒物排放浓度,目前最为理想的办法就是在脱硫后增加湿式电除尘对脱硫后的颗粒物进行捕集,以降低出口颗粒物排放浓度。在原有脱硫塔身增加相关设备,必须经过脱硫塔承载力测算。经过测算在原有塔身增加相应的喷淋层及湿式电除尘器,使塔身能满足承载力要求。
在脱硫塔内原有三层喷淋的基础之上增加一层喷淋,在新增喷淋层支撑梁上安装新增喷淋层,增加一层喷淋层,流量2520m3/h;新装喷淋层安装单向碳化硅喷嘴,新增循环泵安装于现循环泵与综合楼之间空地位置,新增循环泵接入口考虑到搅拌器的影响,吸入口应避开搅拌器,并在吸入管上侧空问安装跨管钢梯以便搅拌器检修。
某厂265m2烧结机烟气脱硫建成于2012年5月,采用最为成熟的石灰.石膏湿法脱硫工艺,建成以来运行稳定,排放达标。但2015年1月1日起,省烧结机执行新的排放标准,要求颗粒物30mg/nm3,二氧化硫100mg/nm3,氮氧化物300mg/nm3,通过烧结原燃料入口硫份控制,配合脱硫系统调整颗粒物、二氧化硫连续稳定达标排放,特别是2017年起执行更严格的排放标准,要求颗粒物20mg/nm3,二氧化硫100mg/nm3,氮氧化物300mg/nm3,原有的脱硫设施达不到新标准要求,必须实施脱硫提效改造。改造过程中烧结机需要停机,所以改造方案必须尽量缩短烧结机的停机时间,同时考虑原有设备的利用以降低投资费用。
由于需新增湿式除尘器,脱硫出口雾滴浓度要求可降低,将除雾负荷转至湿式除尘器,故可拆除一层除雾器,降低吸收塔运行阻力,同时可为新增喷淋层安排出装空间,避免吸收塔体整体切割。同时拆除本层除雾器支撑梁。